
ENGINEERED SEALING PRODUCTS INC.
SERVICES:
Over the past twenty-five years, Engineered Sealing Products, Inc. has built a solid reputation of providing high quality products, competitively priced, and on time, for a wide range of industries. We primarily focus on high end plastic and rubber components. We find that often there are several methods of manufacture that will yield the same result. However, variables such as deadline, material, size, shape, quantity, etc. will determine the most practical means of production. We offer numerous service options that will guarantee that your project is produced by the method that most efficiently meets the jobs demands. Our services include, but are not limited to: Friendly Knowledgeable Staff, Solution Driven Rapid Response, Expediting, Design, Consulting CNC Machining, Milling, and Routing of both Polymers and Elastomers Compression Molding of TFE and TFE blends Injection Molding of PEEK and PEEK blends, large inventory Compression molding and extruding of rubber compounds Stamping, Die-Cutting, and Slitting of most non metallic materials Assembly, Fabricating, Kiting

We offer combined experience of well over one-hundred years supplying high quality machined components for nearly every industry imaginable. Our CNC machines are among the most current models available today. Not only do we work with rigid polymers, we can also machine rubber. We can supply machined parts from less than one quarter of an inch, to in excess of ninety-six inches. We also offer prototyping and expedited services.

Our extensive selection of mold sizes, enables us to create the ideal size of rods or tubes from which to most efficiently manufacture a wide variety of PTFE components. Combining PTFE resin with various fillers can dramatically alter specific physical properties of achieve a desired result. We stock dozens of blends appropriate for nearly every application.

Die cutting is a tried and true method for the production of consistent quality parts time after time. We operate small clicker presses, as well as large traversing head machines, capable of cutting parts up to eighty inches wide. We can typically have a die built in just one or two days, at very reasonable cost. Nearly all sheet materials can be die-cut, with low cost set-ups, high yield production, and very short lead times.

Very few rubber molders can make the claim, Made in America; we can and we are proud of that fact. Working with most synthetic and natural rubber compounds, but focusing on the higher end materials like FKM, Aflas, HNBR, and Silicone. Our battery of presses ranging from small to extra large, ensure that your job is ran with the utmost efficiency. Rubber to metal bonding expands our options. Tooling cost is very reasonable and we have one of the shortest lead times in the industry. Give us a try.

Our extruders can push up to a six inch profile from most synthetic compounds. Our options for curing are continuous as well as autoclave. Extrusion dies are very inexpensive relative to compression molds and can be manufactured in just days. Most extruded profiles can be bonded endless to produce seals and gaskets far larger than is possible by traditional molding. Short or long runs are no problem, we have low minimums, quick deliveries, and we are Made in America.

Water cutting offers high precision cutting of a multitude of material types: rigid and flexible, dense and soft, thin and thick. Operated by computer navigated controllers, both small and large parts are quickly programed without additional tooling or mold cost. Our cutters can accommodate material up to sixty inches wide and up to six inches thick. We typically ship orders in less than two weeks, but with our expedite services, we can usually provide what you need, when you need it.
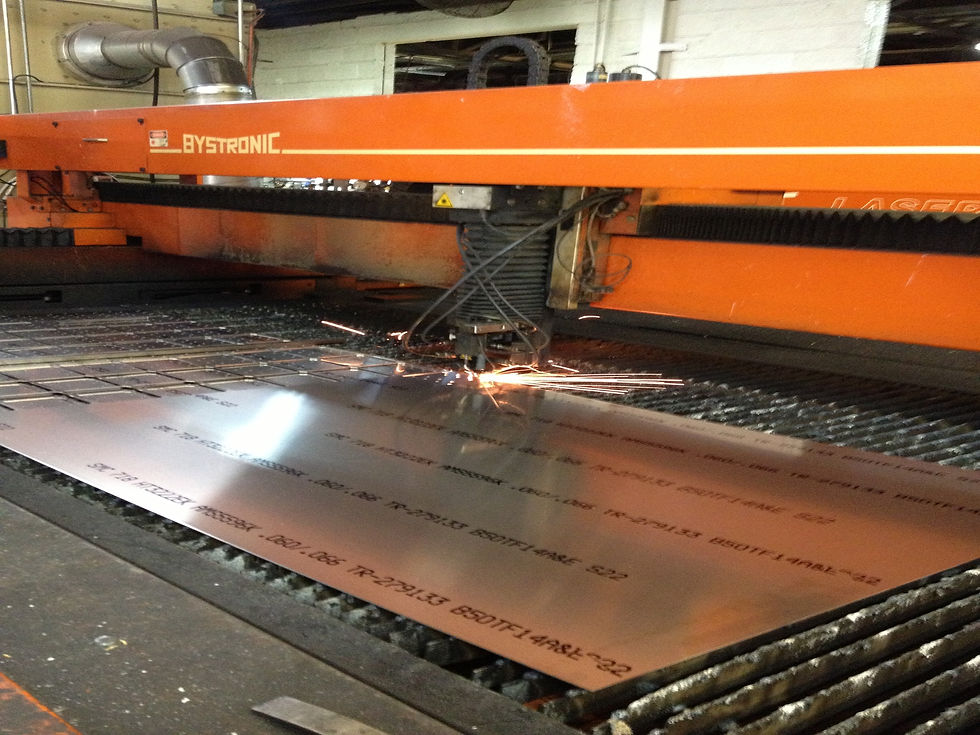
Our laser-cutting service utilizes two sizes of computer controlled laser cutters. Our proto-type cutters can be quickly programmed and offers an economical option for short runs and prototyping of most lighter weight materials. Our production machines are capable of larger runs, with rapid and consistent repeat-ability, allowing us to expand the material options to include heavier materials, such as compressed fiber and steel.

Somewhat different than machining, lathe-cutting is a process by which rubber compound is wrapped onto a steel mandrel, oven-cured, ground to a given diameter and then lathe-cut into a ring which can be used as a gasket, seal, spacer, vibration mount, etc. Due to the speed and automation of this process, it is highly desirable for the production of higher volume runs.

Often an idea goes through numerous evolutions prior to production. With our rapid prototyping service, you can have a working model of each variant in your hands in just a few days. With so many manufacturing tools at our disposal we have the right ones to produce your prototypes, accurately and economically in a time frame that fits your production schedule. ​